Fondazioni profonde: modalità costruttive dei pali di fondazione
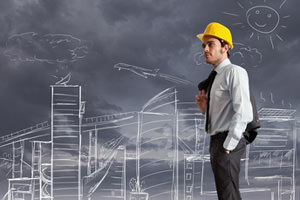
Le fondazioni profonde differiscono da quelle superficiali perché trasmettono la loro sollecitazione oltre che sulla base del palo anche per attrito lungo il fusto. Facendo riferimento alle dimensioni, si dice che una fondazione è profonda quando il rapporto tra lunghezza “L” e diametro “D” è superiore a 10.
E' evidente che una fondazione su pali ha un costo maggiore di una fondazione superficiale; si ricorrerà quindi ad essa quando a) la capacità portante del terreno al disotto della struttura non raggiunge il valore richiesto; b) vi siano delle limitazioni sui cedimenti.
Modalità costruttive dei pali di fondazione
I pali vengono suddivisi in tre categorie:
1. pali prefabbricati ed infissi;
2. pali infissi e costruiti in opera senza asportazione di terreno;
3. pali costruiti in opera con asportazione di terreno (trivellati).
Tale suddivisione è di estrema importanza per il notevole peso che le modalità costruttive hanno nel calcolo della capacità portante.
1. Pali prefabbricati ed infissi
In questa categoria rientrano i pali in cemento armato vibrato, in cemento armato centrifugato e in cemento armato precompresso.
I pali in cemento armato vibrato hanno comunemente sezione quadrata di 20x20 cm o 40x40 cm, armatura con quattro tondi e staffe a spirale a sezione quadrata più fitte verso la punta e la base.
I pali in cemento armato centrifugato vengono costruiti in casseforme metalliche circolari mediante centrifugazione. Essi hanno il vantaggio rispetto ai precedenti di una maggiore lunghezza e la possibilità di essere ispezionati, dopo l’infissione, attraverso il loro foro centrale. La forma è in genere cilindrica o troncoconica con conicità di 1.5 cm/m. Il diametro in punta è in genere compreso tra 22 cm e 30 cm con lunghezze dei pali rispettivamente comprese tra 5 e 27 m. In una sezione ortogonale all'asse del palo lo spessore dell'anello è variabile tra 1/4 ed 1/6 del diametro.
L'armatura viene realizzata ponendo nella cassaforma una barra guida alla quale vengono saldati degli anelli trasversali sui quali a loro volta vengono saldati gli altri tondi. Una staffatura a spirale, più fitta in testa ed alla base, completa l’armatura. La punta del palo è normalmente protetta con puntazze di lamiera riempite di calcestruzzo prima di essere poste nella cassaforma; tali puntazze vengono sostituite con altre a seconda del tipo di terreno in cui avviene l'infissione.
Nei casi in cui i pali sono soggetti a trazione si ricorre alla precompressione che può essere eseguita sia nei pali vibrati che nei centrifugati.
L’infissione dei pali viene eseguita a mezzo di battipali. Il tipo di battipali tradizionale, costituito da una mazza a caduta sollevabile con un cavo, è stato oggi sostituito da un battipalo con mazze “Diesel” su mezzo semovente. Nel palo tradizionale si hanno mazze di peso variabile da 1 a 10 ton, altezze di caduta variabile da 1,0 e 1,5 metri con un numero di colpi al minuto tra 10 e 20. Nelle mazze “Diesel” il peso usualmente varia da 1,2 a 6 ton, con energia utile variabile da 2,5 e 30 t·m. Il numero di colpi a palo varia da 40 a 80 al minuto.
Il peso della mazza deve essere scelto in funzione del peso del palo. Più precisamente esso deve essere compreso tra 0.8 e 2 volte il peso del palo. Con battipali tradizionali v'è pure una correlazione tra peso della mazza e carico ammissibile sul palo, carico che non deve superare 20 - 25 volte il peso della mazza. Tale ultima correlazione vi è anche per i battipali “Diesel”, per i quali si consiglia di adottare un carico ammissibile inferiore ad una energia di 20t·m.
Tali limitazioni sono valide per terreni non coesivi dato che per terreni coesivi l'infissione è facilitata dall'azione lubrificante dell'acqua.
Per evitare che l'urto della mazza rovini la testa del palo si interpone una cuffia che ha il compito di aumentare il tempo d'urto smorzandone l'onda. Le cuffie, in genere sono formate da un cilindro di legno duro cerchiato, di altezza pari a 20 - 25 cm e da dischi di legno di pioppo dello spessore di 5 - 8 cm. Per superare banchi compatti di sabbia senza sollecitare eccessivamente il calcestruzzo, si ricorre invece a iniezioni d'acqua.
Durante la battitura è interessante ricavare il diagramma tempo-cedimento. Il cedimento totale ηt è somma del cedimento permanente ηp (chiamato rifiuto) e da una parte elastica ηe che si annulla istantaneamente ed è dovuta all’accorciamento elastico del palo e al cedimento elastico del terreno. Per evitare eccessive tensioni nel palo si devono evitare elevati valori di ηe, valori che indicano che l'energia di infissione viene quasi totalmente assorbita dal palo. Si interrompe quindi la battitura quando il rifiuto diventa inferiore a 2 - 3 mm al colpo ossia per rifiuti di 2.5 cm ogni 10 colpi. Da osservare infine che i pali di questa categoria possono essere infissi obliquamente nel terreno; le inclinazioni massime tra la verticale e l'asse del palo sono di circa 14°.
2. Pali infissi e gettati in opera
Sono pali in calcestruzzo semplice o armato costruiti in opera ed infissi nel terreno; nella maggior parte dei casi essi vengono realizzati con una espansione alla base. I diametri di questi tipi di palo variano usualmente dai 30 ai 60 cm. L'esecuzione del palo prevede prima l'infissione di un tubo di spessore variabile tra i 20 ed 30 cm e quindi l’esecuzione del getto.
La fase di infissione del tubo può essere condotta in due distinti modi. Si può chiudere con una puntazza la base del tubo ottenendo la sua infissione nel terreno con battitura con martello “Diesel” in testa. Il secondo metodo è quello usato dalla “Franki” in cui viene prima realizzato un tappo di calcestruzzo, ghiaia o sabbia alla base del palo per un'altezza circa pari a tre volte il diametro e quindi si esegue il costipamento con un maglio formato da un cilindro di acciaio del peso di alcune tonnellate di diametro da 20 a 40 cm ed altezza da 5 a 6 m sollevato da una fune e quindi lasciato cadere.
L'infissione del tubo nel terreno avviene per azione del maglio sul materiale che forma il tappo che è impedito ad uscire dal tubo sia per 1’attrito con la parete interna del tubo, sia per l'azione esercitata dal terreno sottostante.
Dopo aver ottenuto l'infissione del tubo sino alla profondità voluta si solleva leggermente il tubo stesso, lo si ancora alla macchina e con alcuni colpi di maglio si elimina il tappo che per il vuoto creato dal sollevamento del tubo, adesso oppone la sola resistenza di attrito laterale. Realizzata tale operazione si inizia il getto del palo. L'espansione di base viene ottenuta immergendo nel tubo piccole dosi di calcestruzzo confezionato con la minima quantità di acqua per far presa e battendo su di esso con il maglio. Una quantità di acqua superiore, farebbe penetrare il maglio nel calcestruzzo rendendo difficoltosa od impossibile la formazione del bulbo di base.
Ultimata la realizzazione della base si passa al l'esecuzione del fusto che può essere eseguita con il metodo del palo colato o con il metodo del palo battuto, scegliendo l'uno o l’altro principalmente in relazione alle caratteristiche geotecniche del terreno in cui il palo è immerso.
Il palo colato viene eseguito riempiendo intermente il tubo con calcestruzzo di grande lavorabilità dosato a 350 kg/mc di cemento; tale fase deve essere rapida e richiede quindi l'approvvigionamento preventivo della necessaria quantità di calcestruzzo. Ultimato il riempimento si estrae il tubo.
Il palo battuto viene invece realizzato immettendo nel tubo calcestruzzo dosato a 300 kg/mc di cemento a dosi successive, battendo con il maglio ed estraendo gradualmente il tubo.
La quantità ottimale di calcestruzzo da immettere è quella corrispondente ad una altezza nel tubo pari a 50/70 cm; si appoggia quindi il maglio sul calcestruzzo tenendo la fune in tensione e si solleva il tubo di circa 30-35 cm e si batte quindi con il maglio.
Durante l'estrazione del tubo il calcestruzzo, spinto dal peso del maglio, occupa il foro abbandonato dal tubo e viene quindi successivamente pressato entro il terreno della battitura. Le fasi di lavoro citato vengono ripetute fino alla completa esecuzione del palo.
Come sì vede i due metodi di esecuzione del getto differiscono notevolmente tra di loro sia per la metodologia sia per il materiale. Con il palo battuto il calcestruzzo viene spinto contro il terreno per effetto del maglio mentre tale spinta nel palo colato è solo dipendente dal peso del palo stesso. In linea generale quindi si dovrà adottare il palo colato in terreni molli per i quali l'uso di un palo battuto può dare come risultato un palo molto deformato, asimmetrico o addirittura con asse non rettilineo per la scarsa e non costante resistenza che il terreno offre al calcestruzzo spinto contro esso.
Le lunghezze dei pali usuali sono dell'ordine dei 25 metri anche se con particolari accorgimenti e in alcuni tipi di terreno si può arrivare a pali di 35-40 metri. E' possibile anche eseguire pali inclinati sulla verticale con angoli fino a 15°. Per pali di lunghezza superiore ai 15 m è necessario armare il palo per tutta la sua lunghezza con una gabbia formata da almeno 5 ferri longitudinali di diametro variabile da 16 a 20 mm in funzione del diametro del palo, staffati da un'elica. Le dimensioni esterne della gabbia di armatura devono essere di poco inferiori a quelle interne del tubo. Tale armatura può però rendersi necessaria anche per pali di lunghezza minore in relazione al tipo di terreno in cui il palo è eseguito dal momento che la esigenza di armare il palo è dettata dalle modalità esecutive.
In assenza di gabbia di armatura, quando si estrae il tubo durante il getto, il calcestruzzo tende ad essere spinto in su, sia per l'attrito con le pareti interne del tubo, sia per l'azione spingente del terreno su di esso con una conseguente diminuzione di sezione del palo. Tale movimento è contrastato dal peso del maglio. La gabbia di armatura tende ad annullare la componente di attrito con le pareti interne del tubo trattenendo il calcestruzzo; la sua funzione è quindi particolarmente utile in pali battuti per l'elevato attrito tra pareti interne e calcestruzzo mentre è meno utile nei pali colati dove prevale l'effetto della spinta del terreno. Tenendo presente quanto detto per pali di lunghezza inferiore ai 15 metri si può ricorrere a gabbie di armatura negli ultimi 6 metri e si può armare con spezzoni di ferro negli ultimi 2 metri di testa.
3. Pali trivellati
I pali di questo tipo, vengono eseguiti dopo aver praticato un foro nel terreno. Il diametro di un palo trivellato viene in pratica riferito, non alle dimensioni della struttura realizzata, ma a quella dell'utensile di perforazione o del tagliente della camicia metallica. La misura dell'effettivo diametro del palo viene perciò eseguita in corso d'opera attraverso la conoscenza del volume di calcestruzzo richiesto dal palo per ogni metro d'altezza.
I pali con diametro compreso tra 80 e 220 cm vengono usualmente indicati come pali a grande diametro. Questa categoria di pali trova oggi grande applicazione nelle strutture soggette a sensibili sforzi orizzontali.
Le tecniche di perforazione per la realizzazione del pre-foro sono legate alla natura ed al tipo di terreno; esse devono soddisfare alle esigenze legate al minimo disturbo nel terreno.
Il pre-foro può essere eseguito con una delle sotto elencate tecnologie:
I. perforazione con tubo di rivestimento;
II. perforazione senza rivestimento con fanghi bentonitici;
III. perforazione senza rivestimento;
IV. perforazione mista.
In terreni non coesivi sotto falda vanno generalmente impiegate tecniche di perforazione con sostentamento delle pareti del foro mentre in terreni coesivi o rocce, tale accorgimento non è necessario.
I. Perforazione con tubo di rivestimento
L'infissione del tubo di rivestimento può essere eseguita,
a) mediante battitura;
b) con oscillazioni ortogonali all'asse del tubo;
c) con vibratori.
Con i primi due sistemi il tubo viene infisso ad elementi di 2.50 metri di altezza giuntati l'un l'altro con giunti a bicchiere; tale sistema di giunzione tende oggi ad essere eliminato per le strozzature di diametro create all'interno; sì preferisce adottare colonne a doppia parete che eliminano questo grave inconveniente.
Con il sistema di infissione con battitura, sconsigliabile per pali di diametro maggiore di 100 cm, l’asportazione del terreno viene effettuata man mano che procede l'infissione con una sonda con valvola a ciabatta.
Un metodo migliore di infissione si ottiene impiegando una massa oscillante che comunica alla camicia, in vicinanza dell'inizio del foro, dei movimenti ortogonali al suo asse.
La diminuzione dell'attrito laterale fra terreno e tubo fanno rapidamente procedere l'infissione facilitata peraltro dalla forma del tubo, dentato alla base, dal suo peso e dalla massa oscillante ad esso solidale. Anche in questo caso l'asportazione del terreno viene effettuata man mano che procede l'infissione; l’utensile usato è una benna mordente.
Il terzo sistema dì infissione è il più rapido (si ottengono velocità dì infissione dì circa 2 metri al minuto) ma ha lo svantaggio di essere utilizzabile solo in terreno non coesivo sotto falda. Esso inoltre prevede l’uso di colonne non giuntate per la difficoltà che i giunti hanno nel trasmettere le vibrazioni.
Le vibrazioni vengono trasmesse al tubo da un grosso vibratore dotato di due eccentrici che ruotano in senso opposto. A differenza dei primi due sistemi il terreno viene in questo caso asportato a infissione avvenuta con un utensile del tipo già visto o con una trivella ad elica.
Una fase importante nei tre tipi di perforazione illustrati è la pulizia del fondo del foro, di notevole importanza, specie in roccia per la mobilizzazione della resistenza di punta del palo. Tale operazione, che in genere non è possibile con i normali utensili usati per l'asportazione del terreno, viene preferibilmente eseguita con un iniettore ad aria compressa facendo trasportare i detriti dall’acqua di falda che usualmente sta al fondo del foro.
II. Perforazione senza rivestimento con fanghi bentonitici
Con il nome di bentonite si indica una argilla del gruppo montmorillonitico caratterizzata da particolari proprietà colloidali. I fanghi formati da un impasto di 1m3 d'acqua e 60-120 Kg dì tale materiale vengono usati per stabilizzare le pareti di uno scavo.
Il meccanismo con cui si realizza il sostentamento delle pareti è il seguente: per effetto della maggior spinta del fango rispetto a quella dell’acqua si forma sulle pareti del foro una pellicola di materiale che riveste il foro stesso. Tale pellicola è formata dalle particelle del fango che tendono a filtrare dal foro nel terreno e sono da questo trattenute; lo spessore del rivestimento varia da pochi millimetri a qualche centimetro con i valori maggiori nei terreni più permeabili.
L'impianto per la preparazione dei fanghi è formato da una vasca della capacità di 20-30 m3 con agitatore; da qui i fanghi vengono direttamente immersi nel foro. Una pompa autoadescante preleva quindi il fango dal foro inviandolo nel foro successivo o in una seconda vasca in cui i fanghi vengono depurati e rigenerati per poi rientrare nuovamente in circolo. La fase di depurazione e rigenerazione viene generalmente eseguita in quei cantieri che prevedono la costruzione di numerosi pali in un'area relativamente ristretta.
La qualità del fango viene in genere controllata in cantiere attraverso la misura della sua viscosità e del contenuto in sabbia. Ambedue le misure sono estremamente semplici; la viscosità si misura con un imbuto della capacità di 1500 cc con al fondo un tubo graduato. Il tempo necessario perché defluisca una prefissata quantità di fango dalla misura della viscosità. Il contenuto in sabbia viene invece determinato con un sabbiometro costituito da una provetta di vetro graduata e da un filtro. La sabbia contenuta nel fango viene trattenuta dal filtro ed il suo valore percentuale viene direttamente letto nel tubo graduato. Il campione di fango da esaminare viene prelevato con una pompa autoadescante dal fondo del foro, punto in cui la sedimentazione è massima. Il valore del contenuto in sabbia deve essere inferiore al 6%; in caso contrario si continua a prelevare fango dal fondo immettendo fango pulito in sommità; tale operazione procede fino a che il valore del contenuto in sabbia, via via determinato, non rientra nei limiti accettabili.
Nel caso in cui i fanghi oltre che sostenere il foro debbano pure portare in sommità i detriti di perforazione si usa il sistema a circolazione rovescia.
Si immettono cioè i fanghi attraverso l'intercapedine tra le aste e la parete del foro facendoli risalire attraverso le aste. In tal modo i fanghi possono acquistare la velocità necessaria per trascinare i detriti nel loro moto attraverso le aste cave che hanno in genere un diametro interno compreso tra 200 e 250 mm. Con lo scavo a circolazione rovescia le tecniche di perforazione in uso sono:
a) a percussione;
b) a rotazione;
c) a roto-percussione.
Con il primo sistema si impiega un utensile di scavo (scalpello) con taglienti infisso a percussione. Il metodo è oggi in uso solo su pali lunghi in roccia.
Nel sistema a rotazione sia le perforatrici che gli scalpelli vengono scelti in base al tipo di terreno. In terreni sciolti, il terreno viene “tagliato” da utensili forniti di lame in rocce si utilizzano scalpelli a rulli conici dentati.
Nella trivellazione a roto-percussione lo scavo viene eseguito con un utensile simile a quello illustrato nel primo sistema infiggendo con percussione e con un moto di rotazione alternata.
Articolo del: